Fill Injectors
KBM fill injectors are superior in several areas, so optimize your production with high performance machinery.
Injektorking fill injectors and accessories are suitable for handling EPS (Styropor/Styrofoam), EPP, EPE, Arcel, Neopor, Graphite etc.
Types of KBM fill injectors
At KBM we have our own brand of fill injectors: the Injektorking series - a trademark for simple and efficient design with quality insurance. KBM offers two different Injektorking fill injectors, each with additional variants. The fill injectors are:
- Injektorking Vario
- Injektorking LS
Within the fill injector category, KBM also offers a selection of quick-clamps (quick-disconnectors), clamp-rings (collars) and Injektorking accessories and spare parts. You can read more about each individual product on their seperate product page listed above.
Benefits of choosing KBM Injektorking
Minimal air consumption
By maximum setting on KBM fill injectors, air consumption is less than half of most other major suppliers of injectors.
Stepless variable adjustment
KBM fill injectors has stepless variable adjustment of the air volume, which means you will never need to introduce more air than needed to fill the mould.
Fast maintenance
It takes just 30 seconds to change the tip to another diameter, and tips are available in all sizes ranging from 18-36mm.
Built-in "blow-back on time"
After closed function, the Injektorking fill injectors have built-in blow-back on time - making sure that no material melts or gets stuck inside the injector barrel after mould filling.
Simple design with extremely low maintenance
To change all wear parts (2 seals) takes 3 minutes. To change the U-seal, which is the only seal inside the steam chamber, takes 15 seconds. All parts are dismantled by hand without the use of any tools.
Designed also for use with pressure filling systems
The KBM Injektorking design is also suitable for use with pressure filling systems. This allows optimal filling - even of thin-walled sections.
Built-in self-cleaning action
A built-in self-cleaning action occurs every time a KBM fill injector is being dismantled after filling a mould; thus making sure it is clean and ready to be used again quickly.
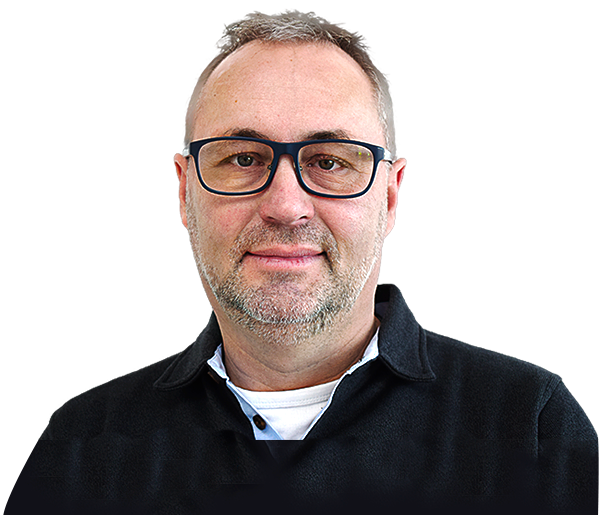